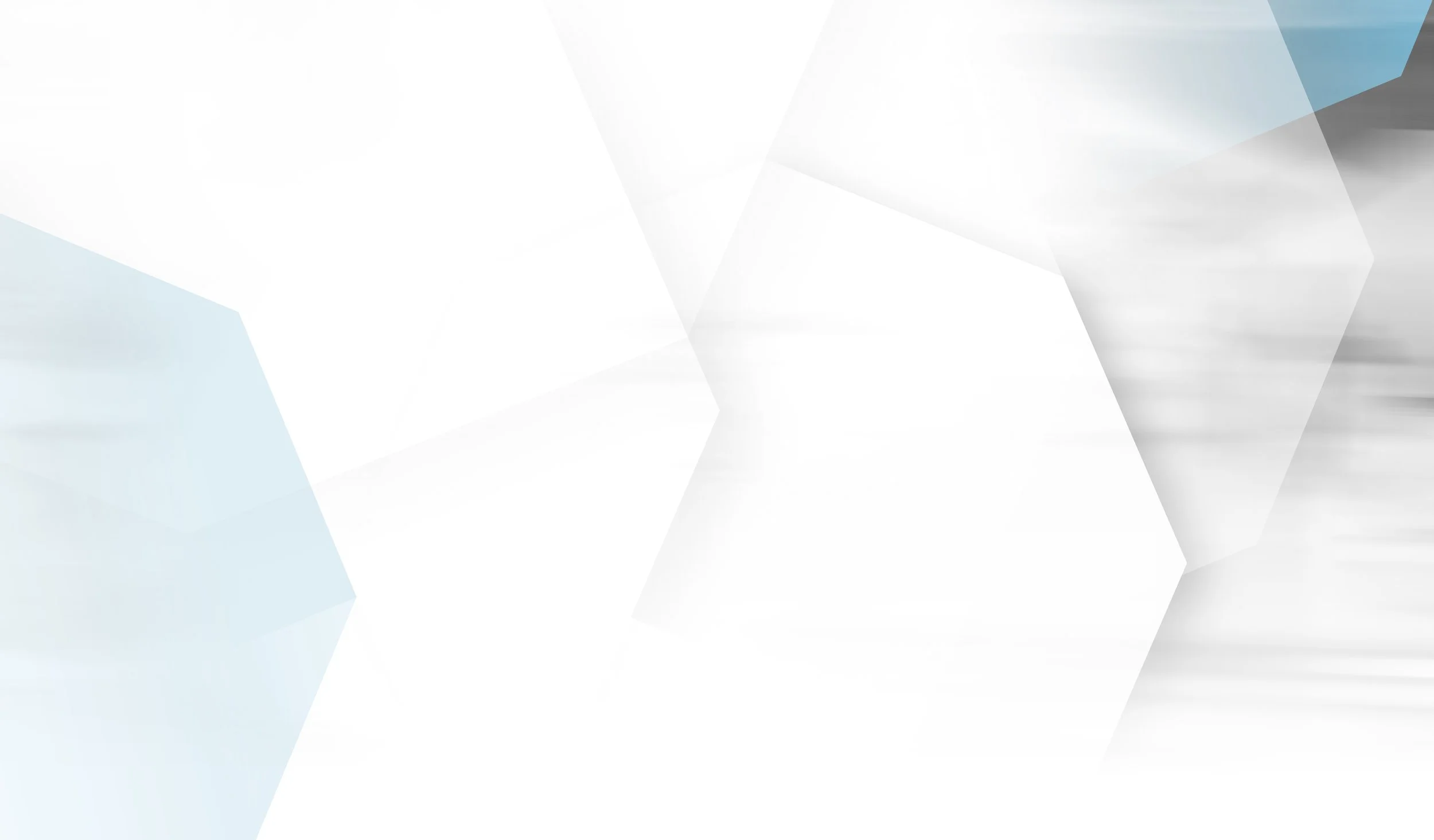
LEETECH
LAMINATOR & LASER EQUIPMENT
Equipment
Laminator & Laser Equipment
Our automation solutions are engineered for speed, precision and repeatability. From fast, efficient loading to consistent temperature and pressure control, our portfolio delivers the capabilities you need to ensure perfection.
-
Download product specifications, datasheets and product brochures:
-
This equipment (LT-081) automatically aligns sheet-type materials. Then utilizes hot roller to perform lamination of dry film that have been cut to fit the pre-set margins of PCBs.
KEY FEATURES
Precise margin control through auto cutting method applying the Servo System
Excellent Lamination adherence by applying D.I Water Station (Optional)
Convenient exchange of dry film and suppliers through Main Body In-out design
The equipment can be entirely controlled at the Touch panel, and provides a highly convenient UI
-
This equipment (LT-050) transports PCB and dry film supplied by temporary laminator using carrier film to chamber to make the inside of chamber vacuum, conduct the perfect lamination by using silicon diaphragm and compressed air and adding heat and pressure.
KEY FEATURES
Adopting diaphragm + compressed air pressure adding system can secure the production of high quality products and high productivity
Reasonable maintenance cost of supplies
Easy maintenance by optimized design
All the control is available from touch panel, it provide user’s convenience UI
-
This equipment, LT-101 transports the products provided from temporary laminator and film into the chamber using carrier film Creates vacuum inside the Chamber, then using silicone rubber plate Then performs lamination with heat and pressure to achieve optimal surface flatness in primary and secondary hot press through level heat and pressure.
KEY FEATURES
Enabled to produce products in excellent quality with industry-proven vacuum lamination system (Selected as a World-Class Product)
Pressurization method utilizing 4-set servo system achieve the highest flatness and easy maintenance
Local procurement of expendable parts reduce the maintenance cost to reasonable level
Easier replacement of carrier films compared to competitions, shortening the lead time for a replacement
All subsystems and equipment can be controlled in touch panel providing convenient user-friendly interface
-
This device transfers the product supplied from the temporary laminator to the chamber using a carrier film, makes the inside of the chamber a vacuum state, applies heat and pressure using a diaphram or silicon rubber plate, and in the Hot press stage implements the best surface flatness.
KEY FEATURES
High productivity and high-quality products can be produced with a vacuum lamination system that has already been verified (world-class products)
Group 4 pressurization system enables the best flatness and easy maintenance
Reasonable maintenance costs through localization of consumables
Carrier film exchange is easier than other companies, so exchange time is shortened
The touch panel can control all the equipment and provides user convenient UI
-
This device (LT-056) lets D.I water pass through roll type material, conducts wet lamination of dry fillm by using hot roller
KEY FEATURES
Installing D.I water station can secure the excellent adhesion of lamination
Adopting tension controller and EPC system can secure the high quality of un-winding & re-winding
Optimized design can secure high productivity, low maintenance cost, easy film setting and replacement
Installing back up roller system can secure the excellent adhesion as hot roller is not bent
