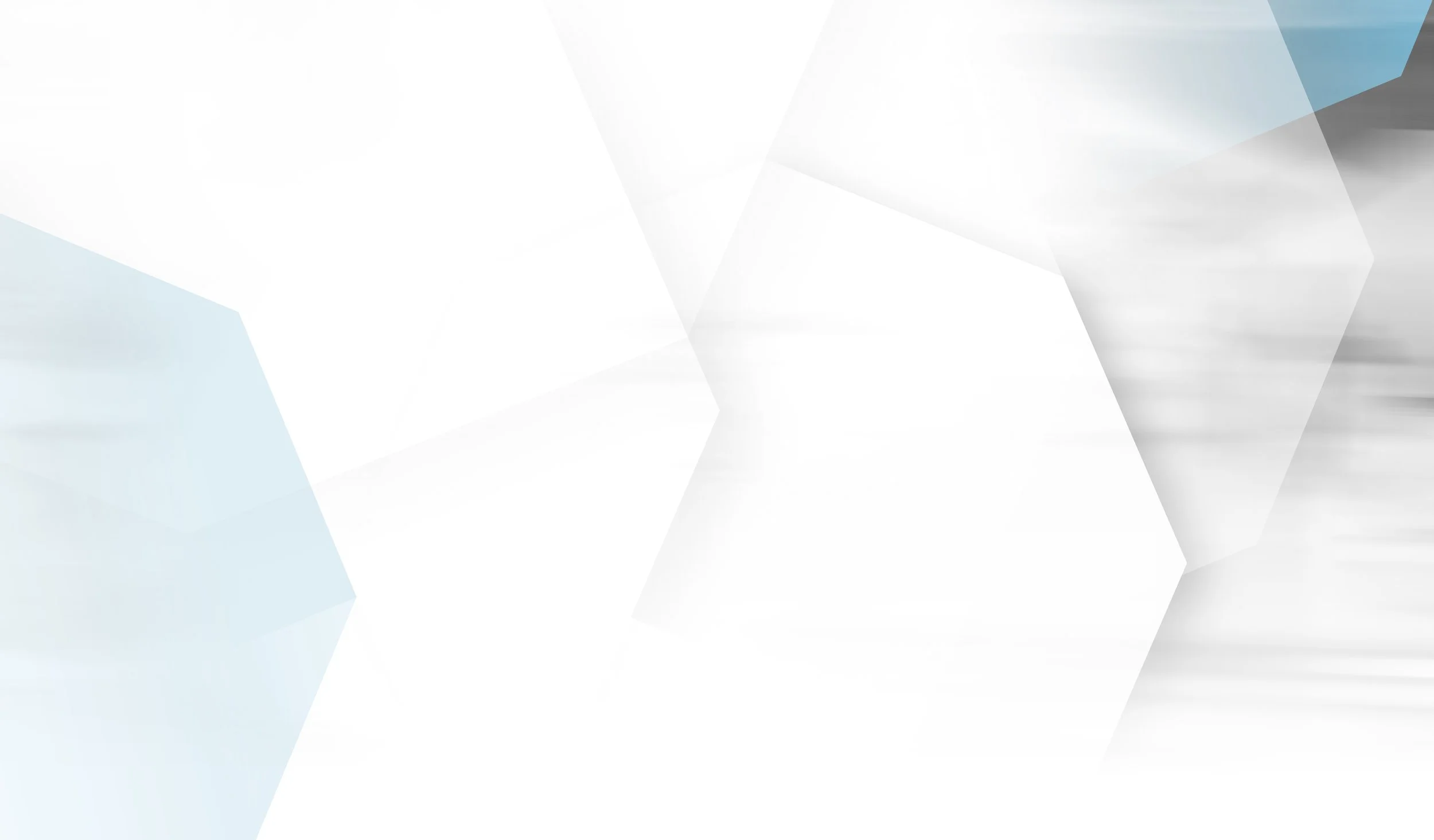
VENTEC GIGA SOLUTIONS PRODUCTION LINE
It ain’t what you do… making PCBs is an age-old art, a proven and trusted recipe recognizable to experts from any era in the history of this vital component. But the specifications and tolerances laid down, the equipment used, the level of automation, the quality of the results expected… well, that’s a different story.
It’s the way you do it. At Ventec Giga Solutions, we not only see technological changes happen, we make them happen. Working with the leading PCB makers and innovative technology suppliers, we guide our customers to make the right investments in state-of-the-art equipment, materials, and processes to keep their capabilities at the cutting edge.
1: PRE-PRODUCTION
We support the entire PCB manufacturing sequence, caring for every process that happens inside your factory to ensure great results. Excellence at the end of the line starts with proper care and attention at the beginning.
PRE-PRODUCTION
PRE-PRODUCTION
2: PHOTO TOOL PREP
Before any materials enter production, imaging equipment must be spotlessly clean. Our complete portfolio of high-speed, high-quality automation solutions has it covered.
YEITEK >
PHOTO TOOL PREP > MACHINE: YEITEK
PHOTO TOOL PREP > MACHINE: YEITEK
3: INNER LAYER PRINTING
The PCB starts taking shape as the circuit features are printed according to CAD data supplied. Automation must provide high positioning accuracy and optical resolution to ensure precision within a few microns; essential to ensure quality and functional integrity of the end product.
INNER LAYER PRINTING > MACHINE: YEITEK / LEETECH
INNER LAYER PRINTING > MACHINE: YEITEK / LEETECH
4: INNER LAYER ETCHING
Etching reveals the structure of each foil layer.
At Ventec Giga Solutions, we can support all etching processes including chemical and laser etching.
TAESUNG >
INNER LAYER ETCHING
INNER LAYER ETCHING
5: AOI
Essential for quality control, automated optical inspection verifies imaging and etching and takes critical measurements. The data captured identifies any defective units and provides vital information for traceability, troubleshooting, and process improvement.
YEITEK >
AOI > MACHINE: YIETEK
AOI > MACHINE: YIETEK
6: LAY-UP
Accurate registration correctly positions individual layers relative to each other, and careful handling preserves the delicate circuit features as the stack is built. Next to accuracy and repeatability, speed is critical to ensure productivity. Also, lay-up provides another opportunity to capture measurement data for process analysis and improvement.
YEITEK > SURGE ROBOTIC >
LAY-UP > MACHINE: YIETEK / SURGE ROBOTIC
LAY-UP > MACHINE: YIETEK / SURGE ROBOTIC
7: LAMINATION
The PCB literally comes together at the lamination stage. Critical process parameters include clamping pressure and temperature, demanding precise control for proper bonding and ultimately ensuring the board’s structural integrity.
FALKENRICH > CARDEL >
LAMINATION > MACHINE: FALKENRICH / CARDEL
LAMINATION > MACHINE: FALKENRICH / CARDEL
8: DRILLING
Drilling begins the sequence of creating vias for intra-layer connections, connecting component terminations to inner layers, and other purposes such as thermal management. Accurate positioning is required, with minimal deviation. High standards are essential in the chosen automation, as significant value has been added to the board by this stage.
DRILLING > FALKENRICH
DRILLING > FALKENRICH
9: DIRECT METALIZATION
DIRECT METALIZATION > MACHINE: TAIYO / SUNUS
DIRECT METALIZATION > MACHINE: TAIYO / SUNUS
10: OUTER LAYER IMAGING
OUTER LAYER IMAGING > MACHINE: YEITEK / LEETECH
OUTER LAYER IMAGING > MACHINE: YEITEK / LEETECH
11: PLATING
Pads and lands are plated with RoHS-compatible metals or alloys, to protect the conductors and promote solderability when components are placed and the board is reflowed. Ventec Giga Solutions’ one-stop-shop capability gives access to high-quality materials, supplied through our unique wholly-owned supply chain, ensuring reliable, timely delivery and dependable provenance.
TAESUNG >
PLATING
PLATING
12: INSPECTION
Giving your factory the best automated optical inspection equipment is a wise investment, the reference on which faith in your products and services is built.
INSPECTION
INSPECTION
13: SOLDER MASKING
SOLDER MASKING > MACHINE: TCA TAIYO / GYEYO / YEITEK / HI-PRINT / TAIYO
SOLDER MASKING > MACHINE: TCA TAIYO / GYEYO / YEITEK / HI-PRINT / TAIYO
14: SURFACE FINISHING
Surface finishing applies human-readable information to your PCB, such as identification marks, serial number, component designators, and any company logos. The board’s appearance and branding are closely linked to quality and customer perception.
TAESUNG >
SURFACE FINISHING
SURFACE FINISHING
15: PROFILING
The final stages of board fabrication comprise cleaning and applying any protective film, ready for shipping. At Ventec Giga Solutions, our agreement with our partner's portfolio of automated equipment for PCB fabrication lets us support PCB fabrication from end to end, including cleaning and protection.
YEITEK >
PROFILING > MACHINE: YEITEK
PROFILING > MACHINE: YEITEK
16: BBT, INSPECT & PACK
Bare-board testing checks for correct connectivity between important terminations on the board, before boards are packed ready for dispatch. Our automated solutions handle these tasks with ease and simplicity.
BBT, INSPECT & PACK
BBT, INSPECT & PACK
